Kenya’s Substandard Cement
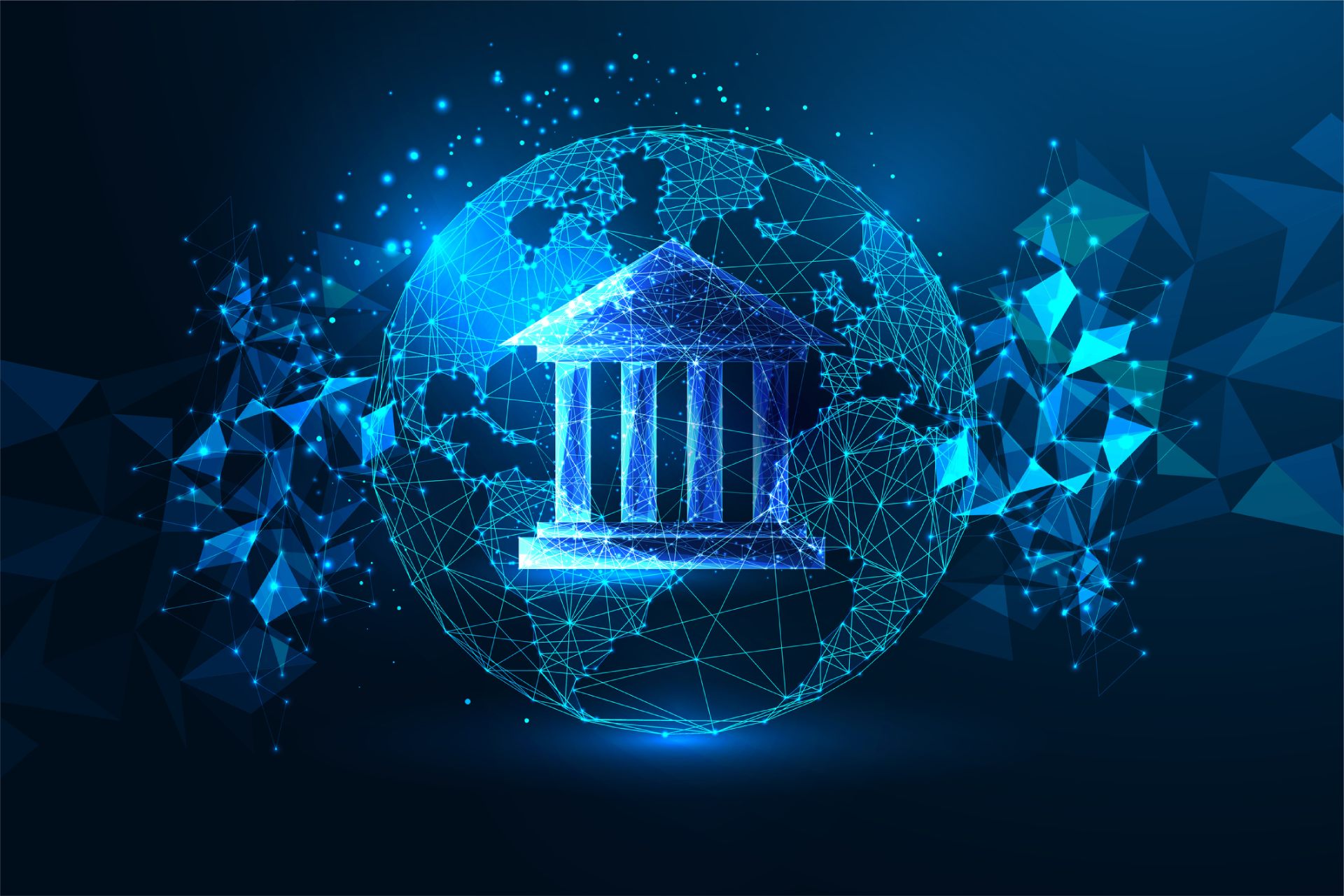
According to a 2022 internal report by the Kenya Bureau of Standards (KEBS), three out of five cement products tested in a market surveillance programme failed the standards tests. The report indicated that only a small percentage of the cement tested in February 2022 met the required standards, including the capacity to withstand the slightest pressure without crumbling. This underscores the urgent need for all stakeholders to adhere to quality standards in the construction industry.
The KEBS report corroborates a 2020 research by the National Construction Authority (NCA), which revealed that about 10,791 buildings were unsafe and not fit for habitation. This came on the backdrop of collapsing buildings, particularly in residential areas. Between 2009 and 2019, 86 buildings valued at over KSh 2.4 billion collapsed countrywide. Another report by the NCA revealed that the causes of the collapses were mainly due to technical issues such as substandard materials, mainly cement and steel. One possible cause of substandard cement is the use of poor-quality raw materials such as clinker. Clinker, the main raw material in the manufacturing process and the costliest input has seen unscrupulous players use less of it, resulting in substandard cement.
The high demand for housing in Nairobi has led some property developers to bypass building regulations to reduce costs and increase profits. Additionally, KEBS blamed the proliferation of low-quality cement in the market on manufacturers’ shortcuts and counterfeiting.
KEBS tests cement products on chemical composition, defining acceptable ranges for key chemical compounds in the clinker to ensure that the final cement product is strong and durable. It also conducts scheduled and random spot checks, whereby samples are collected from various retail outlets, construction sites, and manufacturing facilities to ensure a representative cross-section of the market.
Of particular concern is the common-grade cement, known as 32.5R. This type of cement is mostly used to construct residential houses and apartments, which puts households at a higher risk. However, high-grade cement, known as 42.5N, which is used for heavy-duty construction, passed the compressive tests. This class of cement is held to a higher standard as it can withstand higher pressures and loads, which is essential for the construction of mega projects such as roads and bridges.
Subsequent tests by KEBS found that the quality of cement improved, with 63.4% meeting the compressive tests by December 2023. The standards body attributed this to the commendable efforts of manufacturers in enhancing quality control. This revelation comes at a time when President William Ruto’s administration is making an aggressive push for universal home ownership. President Ruto’s government plans to build at least 200,000 housing units annually, a goal that will significantly boost the cement industry.
As part of the remedial measures to safeguard consumers, KEBS is playing a crucial role in conducting ongoing surveillance both at the factory level and in the market. This proactive approach ensures compliance with standards and enforces product recall procedures when necessary. KEBS also noted that the compliance percentage does not directly translate to the entire market but rather to the samples tested during that exercise. This emphasis on continuous monitoring should reassure stakeholders about the safety of construction projects.